Diagzone Xdiag Subscription Renew, LAUNCH LTR-01 RF Sensor, Thinkdiag Renew , Scania SDP3 Installation
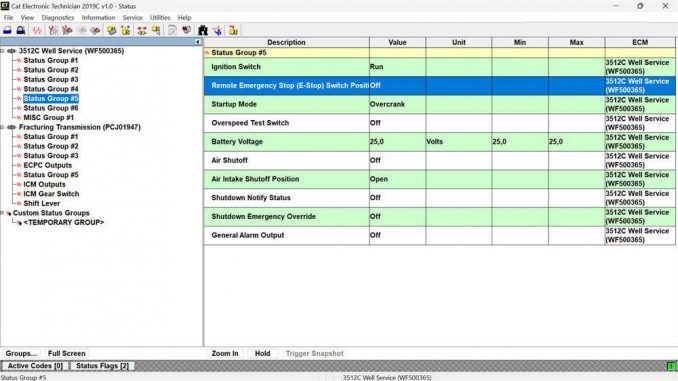
This guide details the diagnostic and repair procedures for addressing the SPN 970 – FMI 2 code, which indicates a fault in the Remote Emergency Stop system on a Caterpillar engine.
Code and Description:
SPN 970 – FMI 2: Remote Emergency Stop Fault, Intermittent, or Malfunctioning
CDL Code: 337-2
Conditions That Cause This Code:
The two inputs from the Emergency Stop switch to the ECM are in opposite states.
System Response:
A diagnostic code is logged when the ECM detects an inconsistency between the signals from the Emergency Stop switch.
How the Emergency Stop Switch Works:
The ECM monitors two signals from the Emergency Stop switch to determine its status.
If both signals are open, the ECM shuts off the engine.
If both signals are connected to the digital return line, the engine continues running.
If the ECM detects mismatched signals at power-up, it logs a fault but allows the engine to continue running. The engine will stop if both signals are open.
Test Steps for Diagnosis and Repair:
Test Step 1: Check for Active Diagnostic Code
Turn the main circuit breaker to the “ON” position.
Start the Caterpillar Electronic Technician (ET) software.
Check for active diagnostic code 337-2.
Expected Result: Diagnostic code 337-2 is not active.
If Not OK: Diagnostic code 337-2 is active.
Repair: The wires between the ECM and the Emergency Stop switch may be reversed or broken.
Turn the main circuit breaker to “OFF”.
Remove the J1/P1 ECM connector.
Measure resistance between P1-23 on the ECM connector and terminal 2 on the Emergency Stop switch.
Measure resistance between P1-28 on the ECM connector and terminal 2 on the Emergency Stop switch.
If an open circuit is detected, repair the wires/connectors.
Test Step 2: Check the Condition of the Emergency Stop Switch
Turn the main circuit breaker to “ON”.
Start the Cat ET software.
Observe the Emergency Stop switch status in the Cat ET.
Activate the Emergency Stop switch (ensure other Emergency Stop switches are not activated).
Expected Result: Emergency Stop switch status is “ON”.
If Not OK: Go to Test Step 4.
Test Step 3: Check the Status of the Emergency Stop Switch When Not Actuated
Disable the Emergency Stop switch (ensure the solenoid valve is retracted and the air shutoff valve is open).
Observe the Emergency Stop switch status in Cat ET.
Expected Result: Emergency Stop switch status is “OFF”.
If Not OK: Go to Test Step 4.
Test Step 4: Test the Operation of the Emergency Stop Switch
Disconnect the cable from terminal 1 of the Emergency Stop switch.
Observe the Emergency Stop switch status in Cat ET.
Install a jumper wire between terminals 1 and 2 on the Emergency Stop switch.
Observe the Emergency Stop switch status in Cat ET.
Disconnect power to the ECM and return cables/connectors to their original configuration.
Expected Result:
If the cable on terminal 1 is disconnected and no jumper cable is installed, the Emergency Stop switch status is “ON”.
If the jumper cable is installed, the Emergency Stop switch status is “OFF”.
If Not OK: The problem is in the wiring between the Emergency Stop switch and the ECM. Go to Test Step 5.
Test Step 5: Install a Jumper Cable from the Emergency Stop Switch to the ECM
Turn the main circuit breaker to “OFF”.
Remove the J1/P1 ECM connector.
Disconnect the F715-PU cable from ECM connector P1-23 and install a jumper cable.
Disconnect the F719-PU cable from ECM connector P1-28 and install a jumper cable.
Remove wire 998-BR from ECM connector P1-5 and install a jumper cable.
Reconnect cable 998-BR into the jumper wire plug in socket P1-5.
Turn the main circuit breaker to “ON”.
Observe the Cat ET Emergency Stop switch status.
Connect the jumper cables in sockets P1-23 and P1-28 to the digital return line in socket P1-5.
Observe the Emergency Stop switch status in Cat ET.
Turn the main circuit breaker to “OFF” and return cables/connectors to their original configuration.
Expected Result:
If the jumper cable is not installed, the Emergency Stop switch status is “ON”.
If the jumper cable is installed, the Emergency Stop switch status is “OFF”.
If Not OK: The problem is with the ECM.
Conclusion:
If the problem is in the ECM or the wiring, replace the ECM or repair the wiring as necessary.
If the Emergency Stop switch is faulty, replace it and confirm the issue is resolved.
Related posts:
How to Change Injectors on a C15 Cat Step-by-Step Guide
Guide to Disassembling and Assembling the 3054C Engine for Caterpillar 312D2 and 313D2 Excavators
Software Configuration Guide: Crushing Transmission TH55
CAT Injector Trim Calibration with Caterpillar ET Software
How useful was this post?
Click on a star to rate it!
Average rating / 5. Vote count:
Please keep this link if you copy the post!